By Lyra Fontaine
Photos by Mark Stone/University of Washington
A team is testing new methods to assess the potential impacts of tidal turbines on marine mammals.
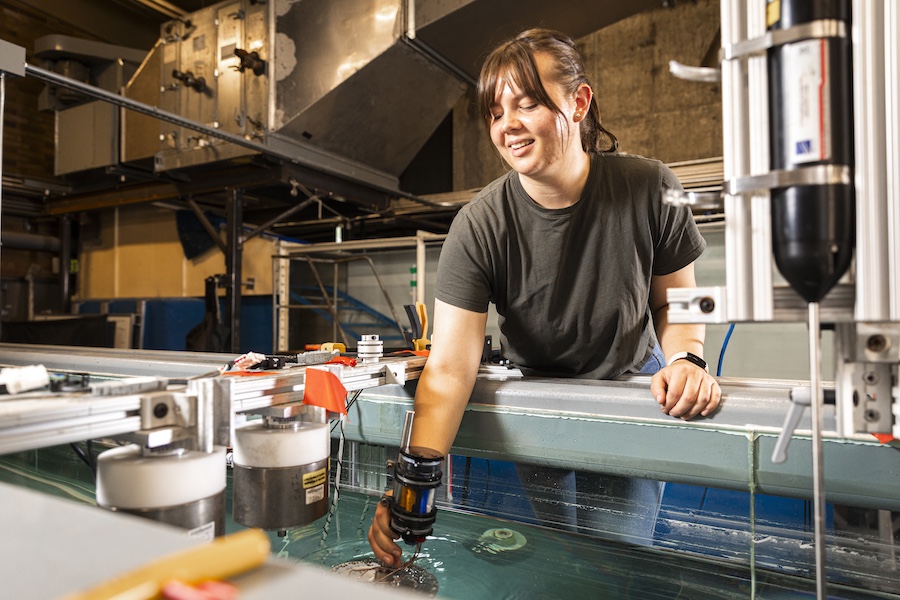
UW research engineer Isabella Pestovski (ME M.S. ’23) places a tidal turbine with sensors mounted to it inside a flume at the Harris Hydraulics Lab.
Marine renewable energy is power generated from the movement of water, such as waves, tides and currents. If harnessed, it could help significantly in meeting energy needs in the United States. Because ocean tides are created by gravitational forces and the Earth’s rotation, tidal energy in particular has the potential to be a consistent and reliable source of power.
One way to convert tidal energy is through a turbine, which can either be suspended from a floating platform or be placed on the seafloor. The motion of tides rotates the turbine’s blades, which then powers a generator.
However, before accelerating the use of turbines and other underwater technologies, regulators and communities want to ensure the safety of tidal turbines on marine mammals. That’s where researchers from the UW and the Pacific Northwest National Laboratory (PNNL) come in.
“It’s exciting to contribute to making sure that renewable energy technologies don’t harm the underwater environment,” says Molly Grear (CEE Ph.D. ’18), a PNNL ocean engineer and ME affiliate faculty member who co-leads the project. “We’re grateful to collaborate with the UW.”
The team – which includes ME alums and affiliate faculty, as well as technical staff members on ME Professor Brian Polagye’s team – is working in a controlled, simulated environment at the Harris Hydraulics Laboratory to assess whether it’s possible to use sensors integrated into turbine blades to detect collision between marine mammals and turbines.
Studies examining the presence and behavior of fish around marine energy devices suggest collisions are rare, but there are still knowledge gaps around the probabilities and consequences of collision events. The researchers hope to develop tools to better understand, and potentially reduce, the impact of turbines on marine life and ensure that testing marine energy devices in the ocean is safe for animals.
The project is a part of PNNL’s Triton Initiative, which conducts research and develops monitoring technologies and methods to understand potential environmental impacts of marine energy devices.
A new way to monitor marine life
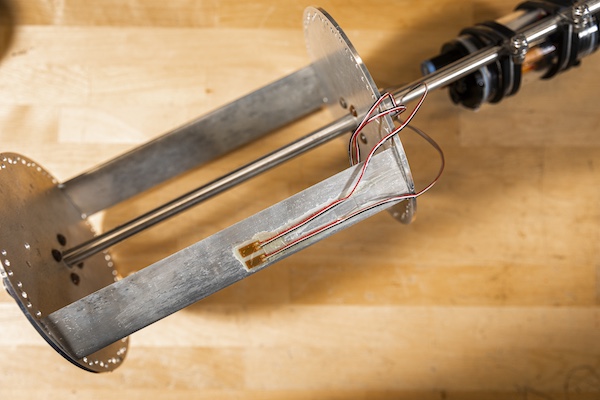
The researchers mounted tiny electrical sensors called strain gauges onto a tidal turbine’s blade.
As a graduate student, Grear researched the potential impacts of turbines on marine mammals by studying their skin and blubber. Through computational modeling, her findings indicated that not all collisions harm animals and that the likelihood of hitting a turbine blade based on animal swimming speeds and rotational rotor speeds are low. The researchers are building on these computer modeling results in the lab by developing new approaches to detect and measure the impact of collisions if they do occur – data that, until now, have been challenging to collect.
“It’s difficult to monitor for collisions, because tidal turbines are typically installed in energetic, hard-to-see environments,” says PNNL and ME ocean engineer Emma Cotter (ME Ph.D. ’19), the project’s co-lead.
The researchers created an experiment to test a new method for detecting collision data, which could someday be used to mitigate collisions and reduce barriers to testing marine energy technologies.
Previous research has developed instrumentation systems to monitor animals at marine renewable energy sites using a variety of sensors, including cameras and imaging sonars. At the UW, Cotter contributed to developing a system that detects underwater marine life at wave and tidal energy sites.
However, acoustic and optical sensors can’t measure the force of a collision, which can provide insight into the level of impact on an animal. That’s why the researchers decided to attach a monitoring system to the turbine itself – a new way of gathering underwater collision data.
They placed tiny electrical sensors called strain gauges, which are typically used to measure the forces on a structure, onto a tidal turbine’s blade. The strain gauges’ voltage changes when force is applied. For example, poking the blade would increase the strain and thus the voltage.
“It felt like a step forward to monitor marine life by using a strain gauge, which might already be on a tidal turbine blade to monitor its performance,” Grear says.
Collecting collision data
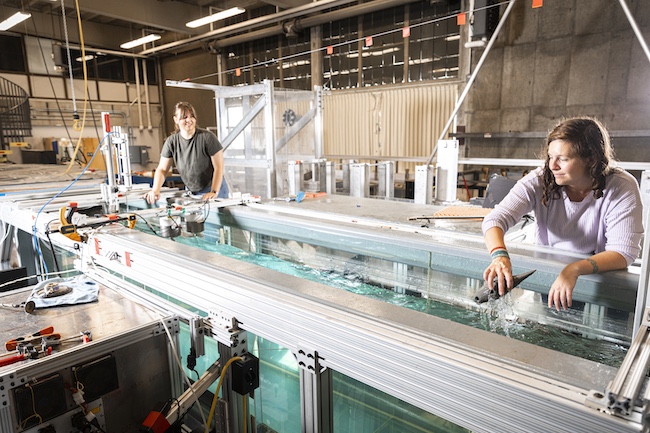
UW and PNNL researchers placed a tidal turbine with sensors, along with a silicone whale model, inside a wave facility at the Harris Hydraulics Lab. They gathered data from the model’s collisions with the turbine, with the goal of making sure that tidal turbines are safe for marine mammals.
The researchers, including UW research engineer Isabella Pestovski (ME M.S. ’23), conducted initial hands-on experiments this past summer to test if the sensors could detect collisions.
They placed the turbine and a silicone whale model nicknamed “Whaleon Jennings” inside a flume, which is a facility with controls for the flow speed, depth and temperature of the water in the tank. Although the silicone whale models don’t represent marine mammal behavior, they allowed the researchers to perform repeatable experiments that simulated the force on the turbine blade if a collision were to occur.
“The goal was to collect the strain data and see to what extent these impacts are detectable,” Pestovski says.
From the experiments, the researchers confirmed that head-on collisions were identifiable in the strain data. The sensors can also potentially detect the presence of an incoming marine mammal since the silicone whale blocked the turbine blade’s fluid flow – similar to a rock blocking water flow in a river.
Skills learned at the UW helped inform the researchers as they prepared for and conducted the experiments. Cotter’s Ph.D. research on environmental monitoring instrumentation provided an understanding of how to work with underwater systems. A ME renewable energy course taught Grear and Cotter about the mechanics of tidal turbines. And Pestovski’s machine learning knowledge enabled her to quantify the force of impacts through data analysis.
Understanding the environmental impacts

The researchers confirmed that the sensors on the blade can identify head-on collisions to the turbine. Eventually, they hope to use the sensors to slow the turbine when the sensors detect the silicone whale model approaching.
The team’s next steps are to improve experimental setup for further research and examine how the data can inform turbine control algorithms to reduce the impact of collisions if they occur. They also plan to investigate how these preliminary results can apply to full-scale turbines deployed in the ocean.
Researchers assessed how marine mammals may be impacted by the spinning blades of tidal turbines.
Early results show it might be possible to use data from the sensors to control the turbine’s operation, so the blades could move at a slower speed when the sensors detect an oncoming collision. This could have less impact on a mammal.
By developing a new approach to detect collisions and measure the potential impact of a blade strike, the team’s research could lower costs and other barriers to testing marine energy technologies.
Throughout the experiment, Pestovski has been drawn to the ability to make a difference in marine energy research, a new challenge for her.
“Before this research, I’d never worked on or considered environmental problems for renewable energy solutions,” she says. “I’m excited to continue to work on this project to help make marine energy technologies more accessible and usable.”
Originally published December 11, 2023